Rotterdam krijgt Fieldlab 3D-printen
Dat is de conclusie na een pilotproject van een jaar in de Rotterdamse haven naar het gebruik van 3D-printers. 28 organisaties uit de maritieme sector hebben in deze pilot in een periode van negen maanden onderzocht of 3D-printen realistische mogelijkheden biedt voor de sector. Het initiatief hiervoor kwam van InnovationQuarter, RDM Makerspace en het Havenbedrijf Rotterdam.
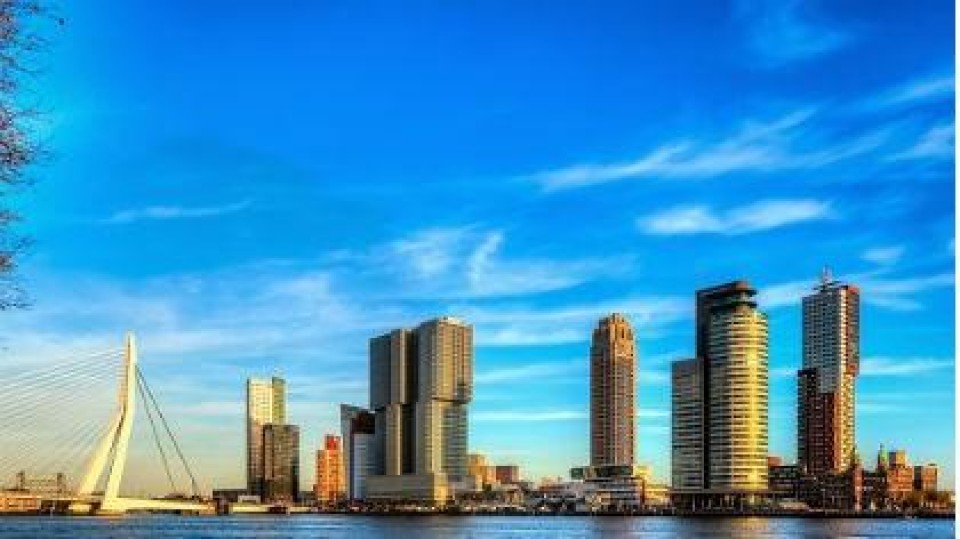